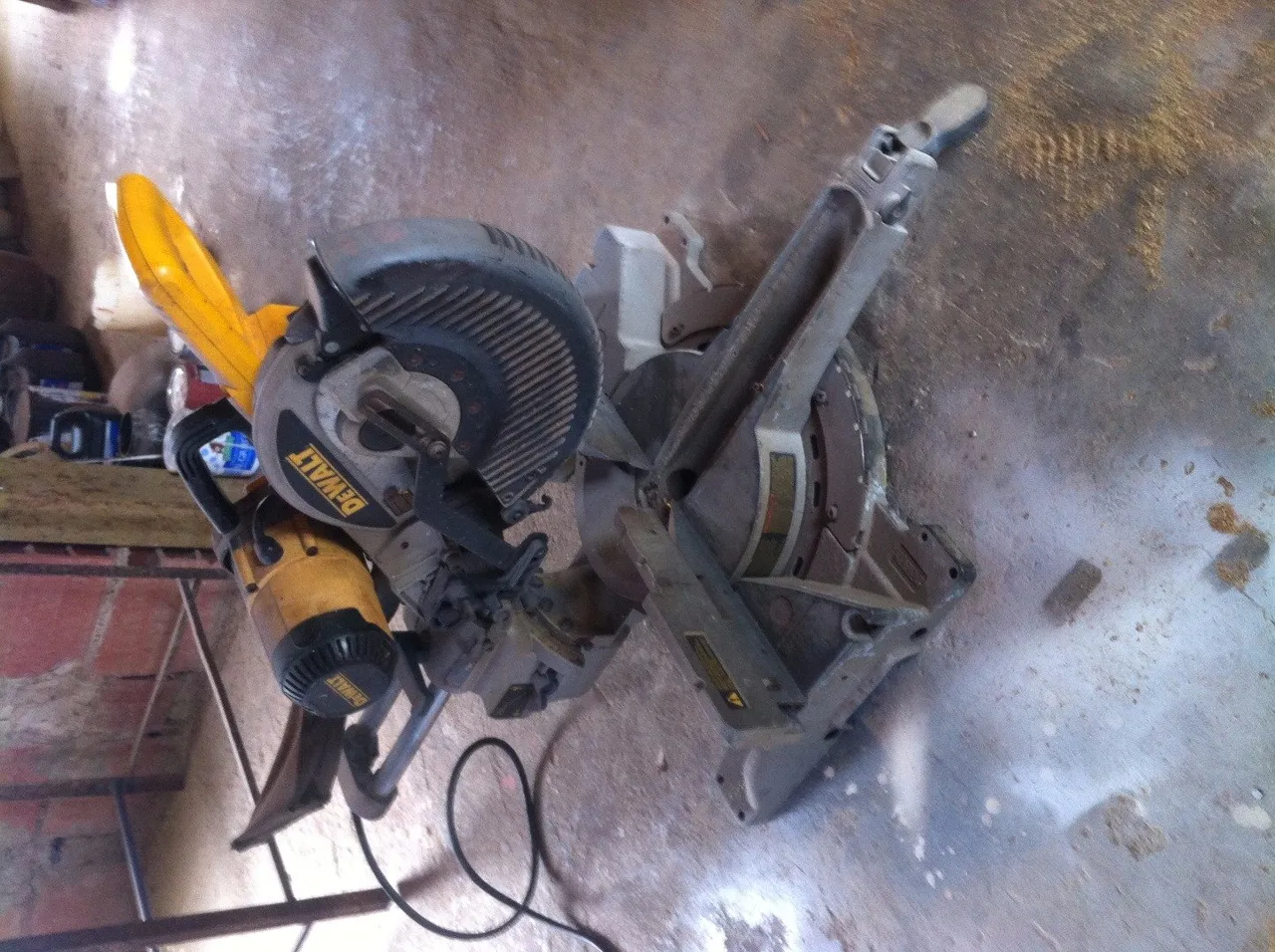
After wracking my brains for an alternative solution I came up with nothing and accepted the inevitable conclusion that in order to complete this job I was going to have to bite the bullet and use my lovely wood saw. Modifications completed I spent the next four days cutting all the pieces then three more cleaning all the rough edges and preparing the cuts for welding. I made a set of jigs (sort of moulds or guides useful when making multiples of one shape or size) and prepared everything for the next day when I would begin to weld.
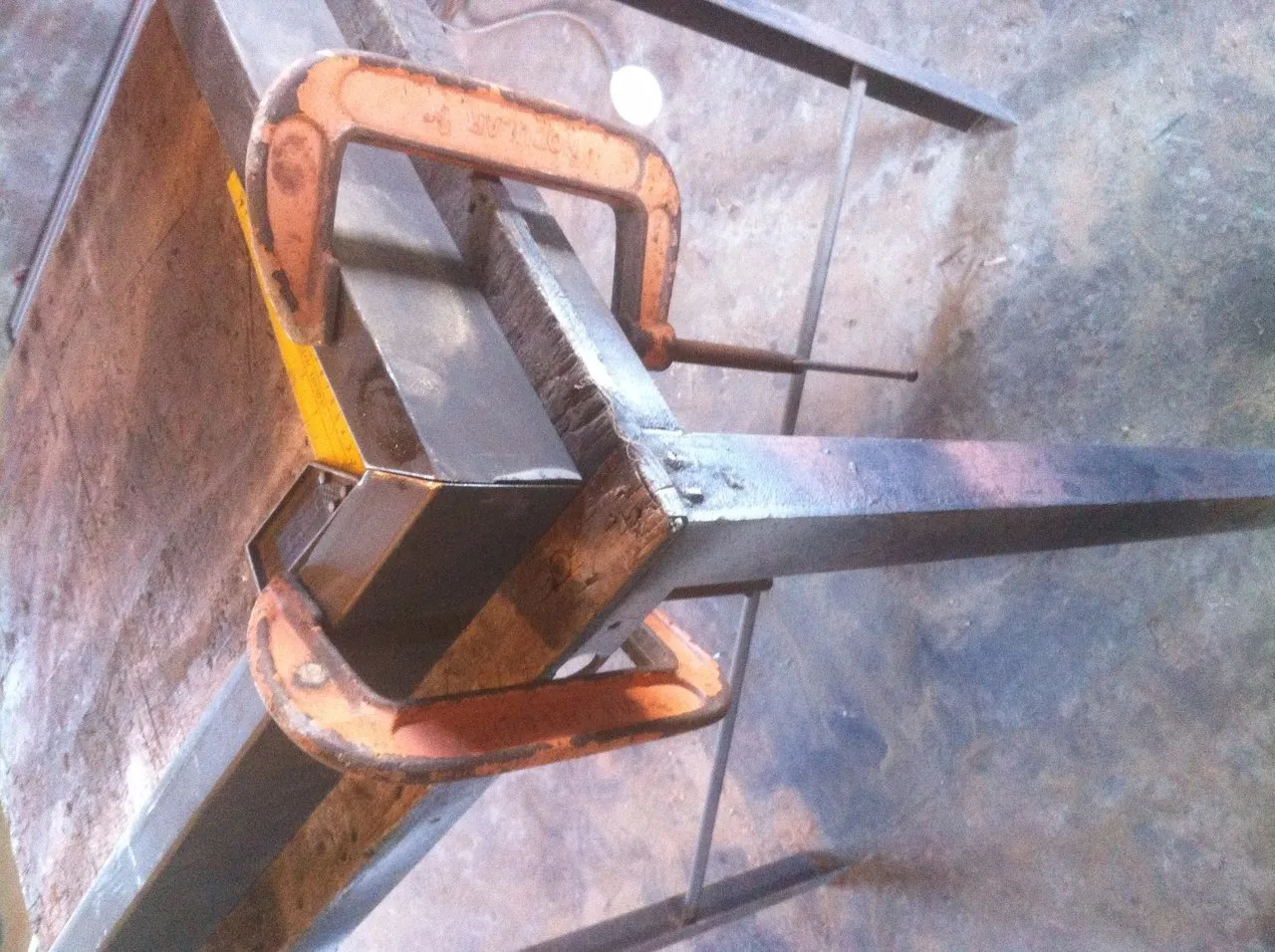
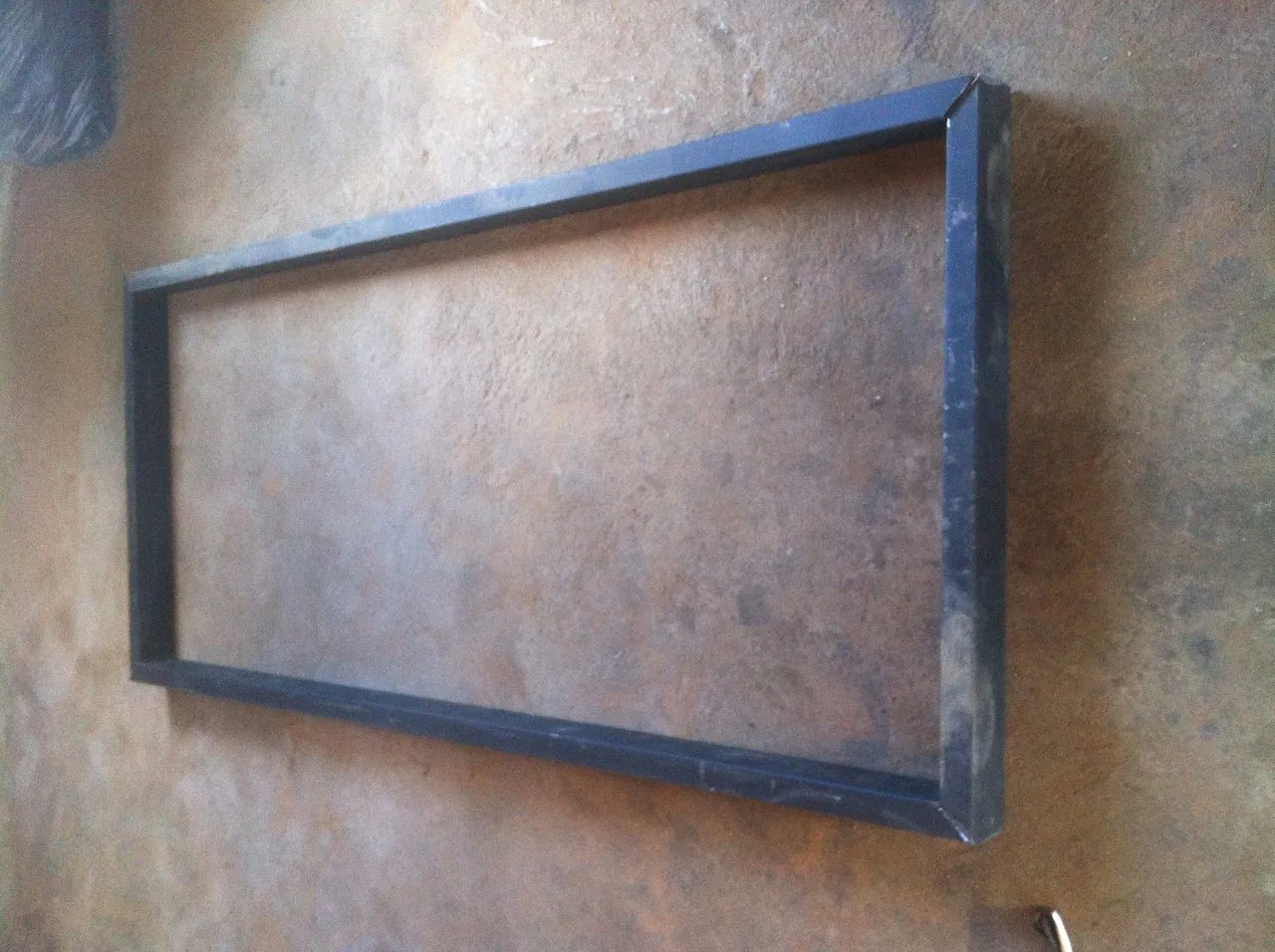
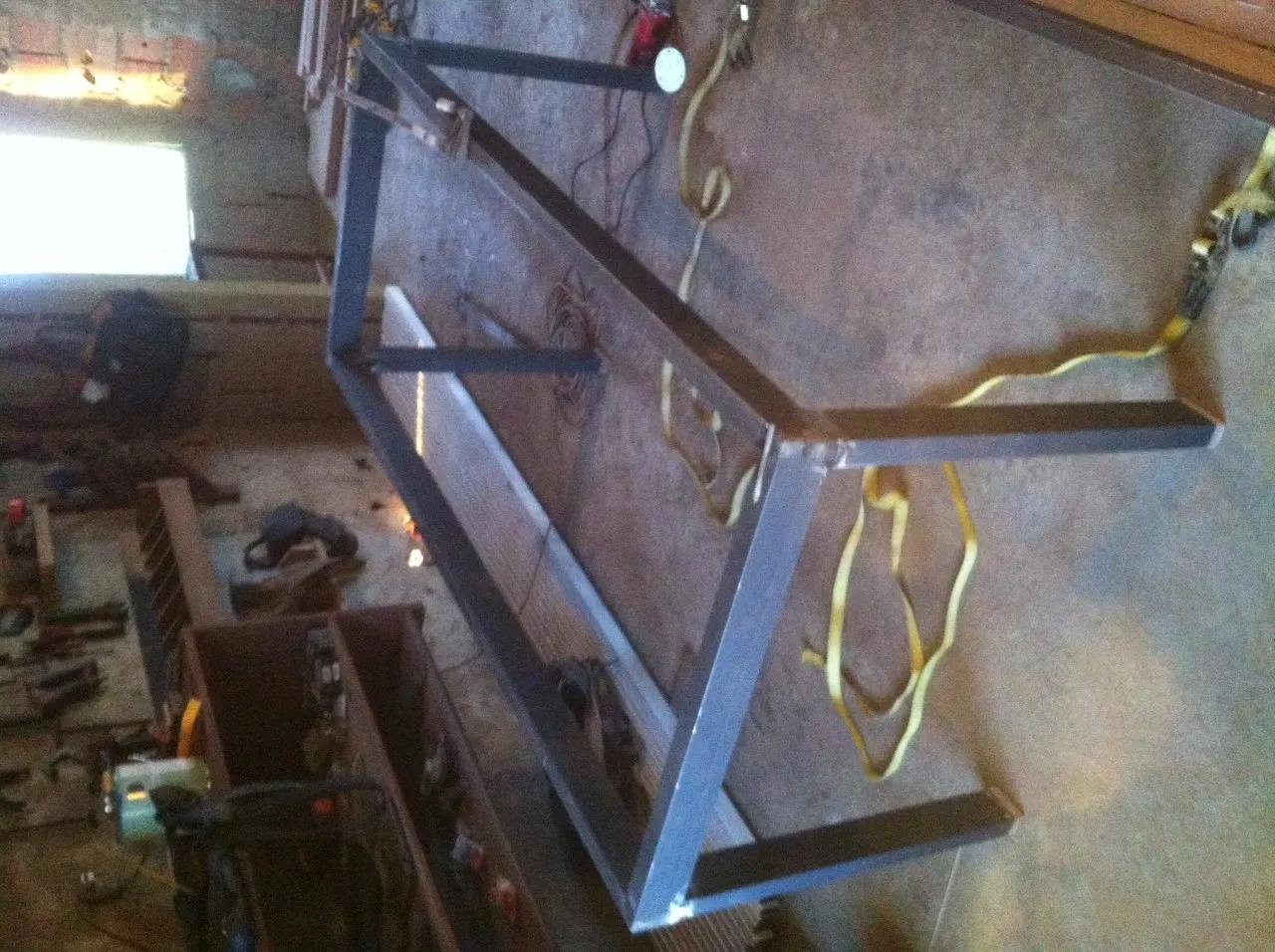
The next day or so was spent grinding the welds and preparing the surfaces for bondo (a resin based filler such as is used in automotive body repairs). I had managed to find a gallon of the aforementioned filler; it is in short supply, in fact completely unavailable for the greater part of last year. As I said, I found some in a back street hardware store so with the surfaces ground down as far as was required I applied a generous coating of bondo and left it to cure.
Having not hit the water for a couple of weeks I took this opportunity to do a bit of kite surfing.
The next day I entered the workshop fully expecting to spend the day sanding the bonded surfaces but was dismayed to see that the bondo hadn’t cured at all.
It shames me to admit that I yelled a few creative obscenities at the table and wasted a few minutes reading the tin of bondo to get some idea as to why it wouldn’t cure. All I could come up with was that it was either due to the humidity in the air this close to the sea, though I had used this product here before without problems, or the hardener was out of date, or a combination of factors unknown. Either way I had to find a solution.
I called up my friendly taxi driver and we headed out in search of an open hardware store. It took most of the day and covering most of the island but we finally found an open store and paid a grossly inflated price for a smaller tin of bondo. I spent the next day cleaning off the old and applying the new. This completed there was nothing to do but wait.
It was with trepidation that I walked into the workshop the following day. To my huge relief the bondo had hardened perfectly so I set to sanding it all smooth.
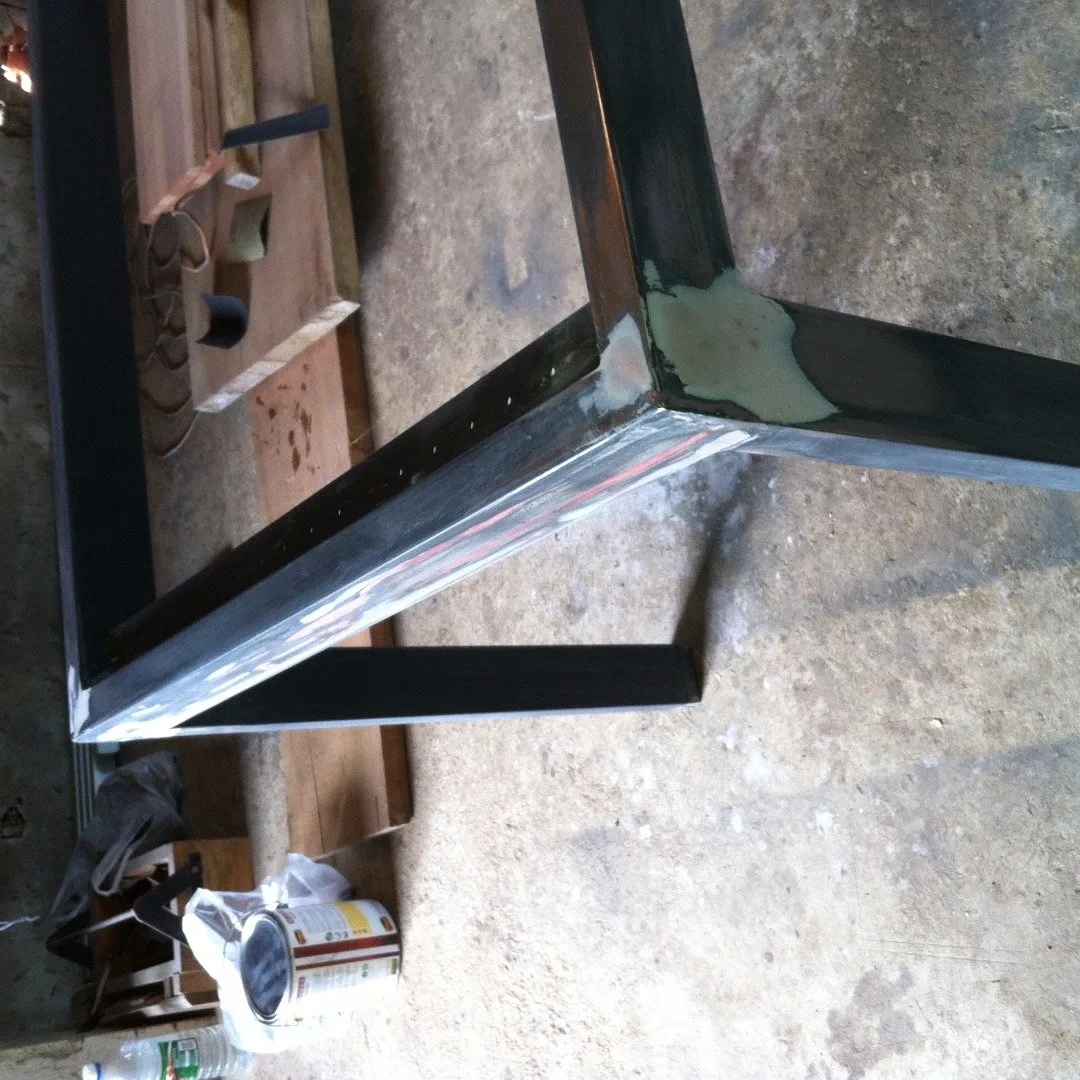
This task completed it was time for another coat of primer.
Whilst running through my preparations and making a test of the paint pistol I saw that the paint was speckled with what looked like oil. I soon discovered that my compressor had a faulty gasket that was allowing oil to seep into the air cylinder. I took this in my stride and made a new gasket from some grease proof paper I had tucked away in storage. This is not the ideal material for making gaskets but I had nothing else I could use and it would last at least as long as I needed to get the job done.
The repairs completed I applied a nice thick coat of primer.
The next day was spent making and fitting the hard wood feet for the table and applying more primer. I like to give each piece at least five coats of primer; the climate here is brutally hot for outside furniture so it is a good idea to give it as much protection as possible.
I would add at this point that the ideal covering for steel in these climes would be simply to powder coat it. Powder coating is a process where ionized plastic dust is applied to metal which is then placed in what is essentially an oven and allowed to cure. The powder forms a liquid in the heat which turns into a durable plastic coating which would be ideal here.
Unfortunately this process is unavailable here so five coats of primer was the order of the day.
Having spent a good few days wielding the grinder, and all the other tools, my arm was getting tired. Not to put too fine a pointy on it I saw the return of Tennis Elbow. For those of you unfamiliar with this; it’s an inflammation of the tendons in the elbow and causes sharp stabs of pain at the most inopportune moments and a general level of discomfort which lends itself not at all to creative endeavours.
I took a few days rest
To be continued......